To manufacture electric cars, Jaguar Land Rover must redesign the factory
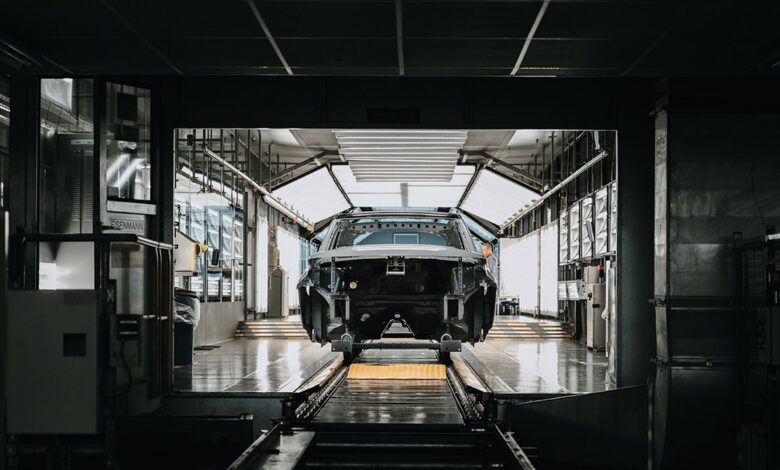
Transforming an auto factory entering its seventh decade into a futuristic facility, ready for AI-powered autonomous driving, comes with natural challenges. Among them: architectural drawings of the 1960s—and the imperial system. “We had to survey everything and go out with a tape measure,” explains Dan Ford, site manager at the Jaguar Land Rover (JLR) site in Halewood, Merseyside, England. “But the measurements on the drawing were wrong: we hit a drain pipe.”
Aside from minor roadblocks (wonderful UK weather and an August downpour that delayed work by 48 hours), the Halewood factory upgrade cost £250m (323.4 million USD) of JLR went smoothly. Off the River Mersey, 10 miles from Liverpool, Halewood has long been synonymous with the British car industry—and JLR is the UK’s largest car employer. (of the company Jaguar Type 00 is controversial will be built at another factory in Solihull). Opened in 1963 by Ford of England to build the Anglia (the small family salon that served as the flying car in Harry Potter series), the plant’s transformation plan began in late 2020. Ford’s team ditched the tape measure in favor of a digital tape measure, scanning an area of 1,000 square meters (10,764 square meters), floor to ceiling, every weekend.
Halewood has now been modified for the cars of the future. A fleet of 750 robots (“our version of the Terracotta Army,” Ford says), laser alignment technology and cloud-based infrastructure along with 3,500 JLR employees on the factory floor, are an additional 32,364 m2 (348,363 sq ft) to accommodate the manufacturer’s products. next generation car. The new calibration rigs measure the responsiveness of a vehicle’s advanced driver assistance systems, such as cameras and sensors. Ford says safety levels can be calibrated for future autonomous driving.
The first phase of Halewood’s redevelopment is the new body factory, with two floors separated by 2.5 meters (eight feet) of concrete to accommodate heavy machinery, capable of producing 500 bodies car every day. The new production line is now in the operational phase: pre-production electric mid-size SUVs will be tested through 2025. Forty new autonomous mobile robots now assist Halewood staff with voltage battery installation High. Other additions include a £10 million ($12.9 million) auto-painted body storage tower, which can hold up to 600 vehicles, retrieved by crane to fulfill timely orders. of customers.
Halewood is JLR’s first all-electric facility. The UK government’s zero-emissions vehicle regulations, part of its plan to transition to a zero-emissions economy, came into force in early 2024—22% of all new car sales must be emission-free. Zero emissions. This law has effectively forced the industry to accelerate electric vehicle production, leading to a ban on the sale of new gasoline vehicles effective in 2035; The EU has similar regulations in place. Each of JLR’s luxury brands will have a pure-electric model by 2030, with the Range Rover Electric to be pre-ordered (the company’s only battery-powered car, the Jaguar I-Pace, launched in 2018). , is discontinued).